Ryetec Industrial Equipment was established in 1992 by Mark Harrison, distributing a range of specialist equipment, from log splitters to mower-collectors, as well as high-specification agricultural machinery like the Gustrower range of fertiliser and lime spreaders and chaser bins, which were added to the range in 2010.
The company’s reputation was built on a personable, honest selling style and strong backup, with Mark cultivating good relationships with medium-sized manufacturers that could react quickly to customer feedback.
As the company moved past 20 years in the industry, two new product ranges were added to the portfolio, pushing Ryetec further into the arable and forage sectors.
In 2016, Mark penned a deal to import the Italian-built Maag no-till drill range, and followed this up by taking on distribution of the Marangon Quickcut wholecrop headers.
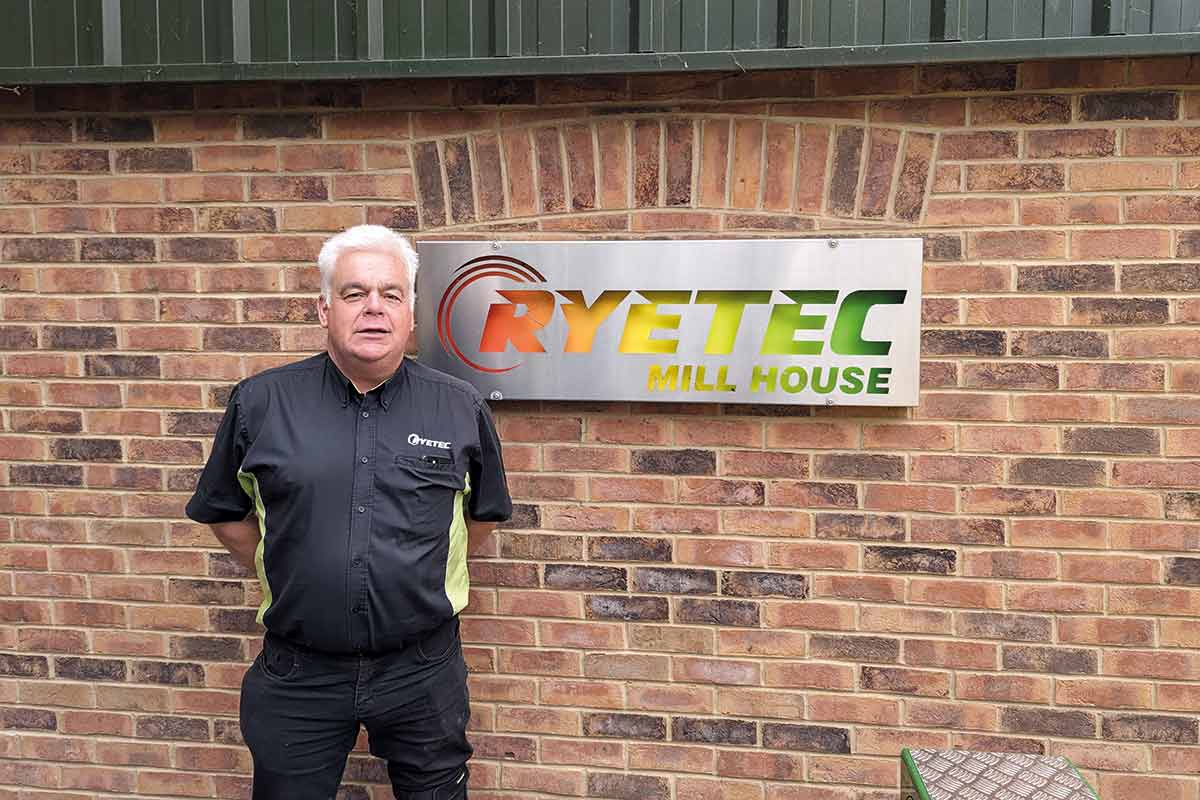
According to sales manager Max Clough, bringing the headers into the UK started the company on a path to set up its own manufacturing base.
“We’d been based at a smaller site previously, but moved to Mill House because it had the space for us to build larger offices and workshops. It increased the covered area fivefold, with a bigger yard and good access from the A64, which makes the larger products easier to deal with” he says.
New premises
The move to Mill House was completed in 2018, initially with just purpose-built offices and workshops. Then, in 2022, Ryetec expanded the site further with its own fully equipped production facility.
The expansion came after a busy couple of years for the company. It introduced its Workbox range of front weights and integrated toolboxes, and then followed this up with the Restorer subsoiler range.
“There’s still so much potential in the Restorer range,” says Mark. “People are just starting to get their heads round what sustainable farming is, and we have double-figure growth year on year.”
A key selling point of the Restorer is its versatility. Ryetec offers several different models to break up compaction in both grassland and arable scenarios.
It’s available as a single unit with a roller to consolidate the soil, or as a toolbar that can be either front or rear mounted (or swapped from one to the other to suit the setup on the day) and can be combined with an additional cultivator or drill for one-pass operations.
Not only that, the 4m and 5m models are built around the same core 3m machine, with hydraulically folding wings adding the width. The design means the machine can work at its maximum width, or at 3m with the
wings folded.
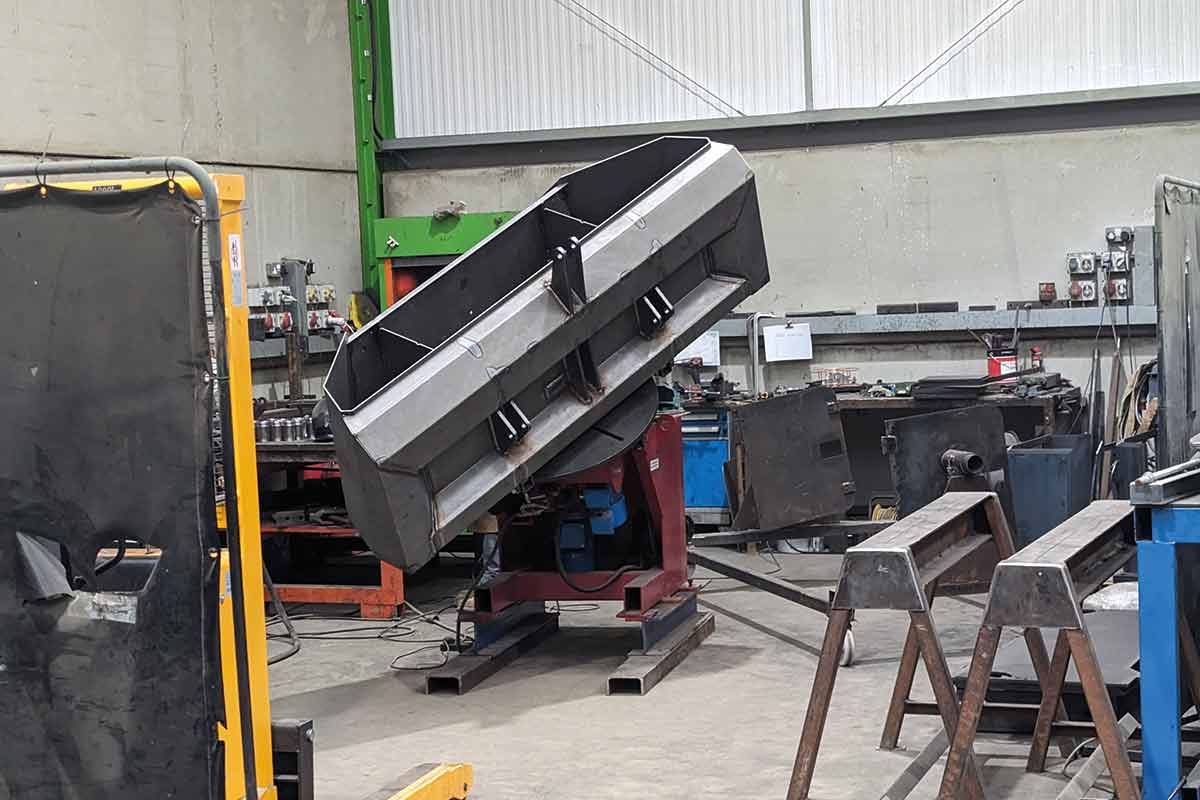
Max explains that this ensures the same quality of work, even when conditions are tricky.
“Especially in a year like this, the headlands can be particularly difficult, but often need remedial work as much, if not more, than the bulk of the field. With the adjustable working width, users can work at 5m in the centre of the field, and fold down to 3m on the headland.”
“It’s about producing a viable crop and looking after the soil by making the least number of passes,” Mark adds.
“We’ve been working with Agrii on various trials and the combination of Restorer and Maag drill has outyielded conventional methods by more than 1t/ha last year.”
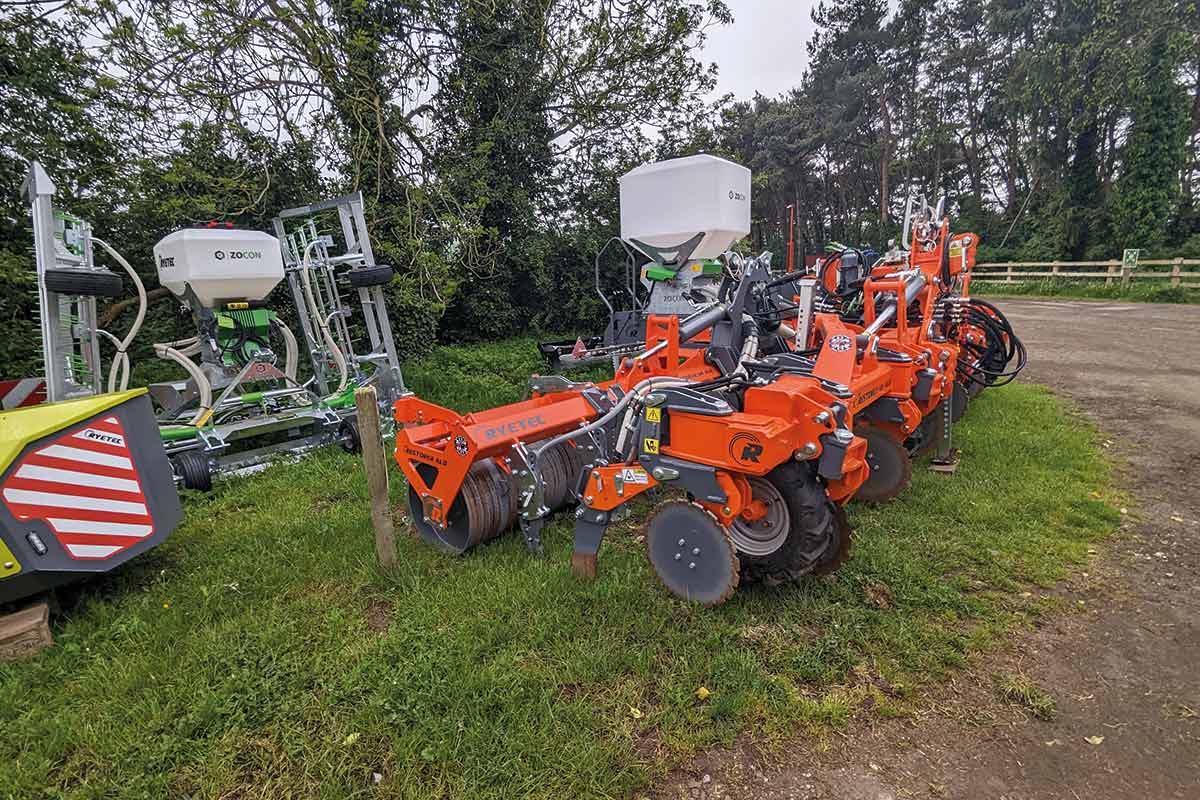
Building up to building
Transitioning from being an importer and distributor, with a small amount of fabrication work, to a fully fledged manufacturer was a massive step for Ryetec – one that saw turnover double in two years and staff numbers jump to 24.
Mark drafted in the help of Shaun Wealleans, founder of Sumo UK, who now designs machines on a freelance basis as Kingfab.
“Working with Shaun really helped us leapfrog to a position in the market where we could be considered alongside more established names,” Mark says.
“By the time he had finished the design, we had a product that was almost market ready. We didn’t prototype as such, instead we started demoing on local farms.
“I went to every single one of those first demos and still go to a lot of them now, and if we do encounter an issue, or a user suggests a change, Shaun is able to turn around new designs in a matter of days. We can offer the right quality without having this massive oil tanker to steer when adjustments are made.”
The success of the Restorer and the Workbox has led to Ryetec developing an arable system for users.
Combined with the Maag drill, the Restorer can be a one-pass establishment tool, and the team are working on disc coulters so that the subsoiler can be combined with a seeder box to establish oilseed rape, biodiversity strips or cover crops.
And in November last year, Ryetec purchased SmartBox, another company offering front-mounted toolboxes with integrated weight blocks.
The range, which is being offered separately from the Workbox and retains its original name, essentially doubled the production of front weights overnight.
“We’ve got five full-time fitters, plus additional welders who come in at peak times, and three people in the paintshop, so the front boxes keep production ticking over through the year,” says Max.
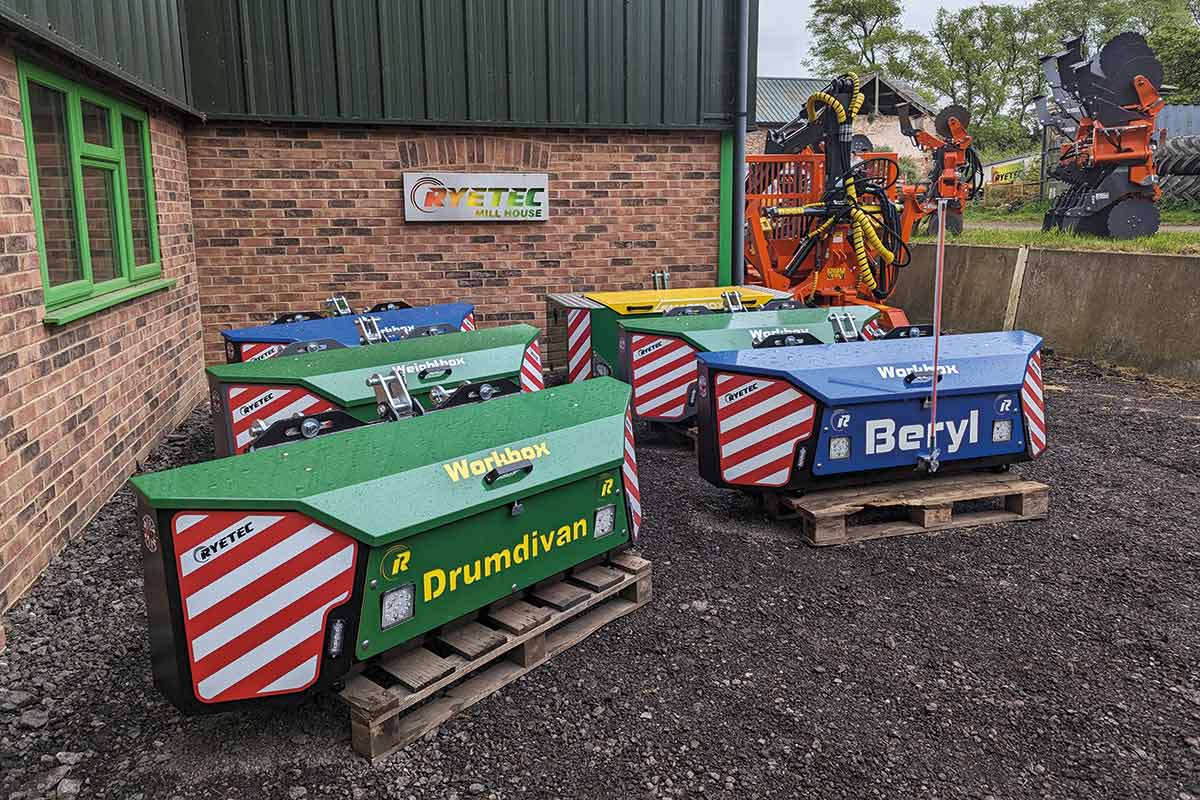
Move to exports
The front boxes have also led to Ryetec exporting its own products to the Continent, a reversal of what had previously happened. “By developing bespoke equipment to suit local farmers, we’ve fallen into markets that had previously been closed off to us,” Mark explains.
“And that isn’t just abroad – interest in the Workbox and the Restorer has seen us grow our dealer network in the UK substantially, which is benefitting our sales of imported goods.”
Now the focus is only finding additional products – either produced in-house or imported – that will complement the existing range.
At Lamma this year, Ryetec announced it would import the Dutch-made Zocon range, which not only adds a line-up of overseeders and mechanical weeding machines to the portfolio, but also gives Ryetec a series of seeder boxes that can be integrated onto the cultivation range.
The extra interest will necessitate further expansion of the site, something that Mark is looking closely at, although he isn’t concerned about outsourcing tasks if it makes economic sense.
“We already have the machining of components done by a local fabricator,” he says.
“Our main concern would be ensuring that we maintain the level of quality we’ve established at this scale and using local businesses to boost employment in our area here in Yorkshire. We’re proud to be building kit in the UK rather than just importing as we were originally – it gives us flexibility to fine-tune machines for the UK market.”