There has never been a better time to invest in CTIS, with systems being covered under the current Farming Investment Fund grant scheme. Grant number FETF109 will cover £3140 of funding towards a CTIS system – accounting for roughly 50% of the total cost. Applications to this scheme are through the www.gov.uk website.
A I Walgate & Son has recorded significant improvements in the health of its soil having equipped its Fendt 724 tractor and two frontline implements with PTG Central Tyre Inflation Systems (CTIS) and Michelin Ultraflex Technology tyres.
The business farms approximately 700 hectares of land in the Lincolnshire Wolds, of which 500 hectares are in arable rotation, concentrating on combinable broadacre crops.
A I Walgate & Son runs Michelin tyres across all its agricultural machinery and is utilising the latest technology from PTG – part of the Michelin Group – to ensure the fitments on its new tractor, Fliegl trailer and Horizon DSX drill are running at optimal pressures for the ground on which they work.
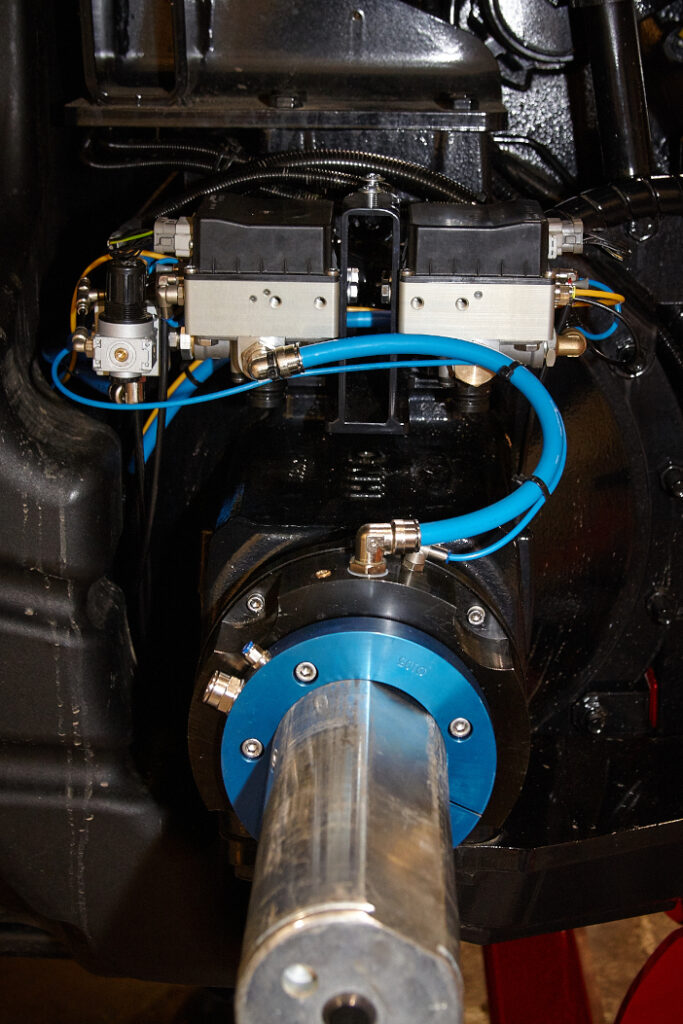
The Fendt 724 tractor is fitted with Michelin XeoBib VF 600/60 R30 front tyres and VF 710/60 R42 rears, while the Fendt 828 is equipped with EvoBib VF 600/70 R30 fronts and VF 710/70 R42 on the rear. The Horizon DSX drill is sat on CargoXBib High Flotation VF 750/60 R30.5 fitments and the trailer is equipped with CargoXBib High Flotation 600/55 R26.5 tyres.
James Walgate, Director of A I Walgate & Son, says: “We’ve been very impressed with the impact of the PTG system. Because we don’t plough anything now, everything is direct drilled, we’re very conscious of wheelings and compaction. This set up really helps in terms of mitigating compaction, which dries the air out of the soil so when it gets waterlogged it more easily becomes anaerobic, which is the last thing you want for your soil health.
“We did some work where we went up the field with the tyres set at road pressures and had half an inch of rain the next night, and you could see the water stood in the wheelings. But when we did the same work with the optimal field pressures there was nothing. The water infiltration rate with the road pressures was calculated to be 8mm an hour compared with 18mm per hour where it had been run with the field pressures.”
The PTG systems were all supplied and fitted by TractAir – Michelin’s approved UK partner for CTIS installation. The farm also has VarioGrip technology on its other Fendt tractor.
“Crucially, TractAir also supplied us with a compressor which we can put on the front of the tractor with VarioGrip to ensure we have the volume of air required for the four tyres on the trailer – because that is constantly going between the road and the field,” adds Walgate.
“We don’t need that capacity on the drill because once we get to the field, we let the tyres down and drill all day. When we want to come home we can blow them up and the VarioGrip on the 828 is good enough for that.”
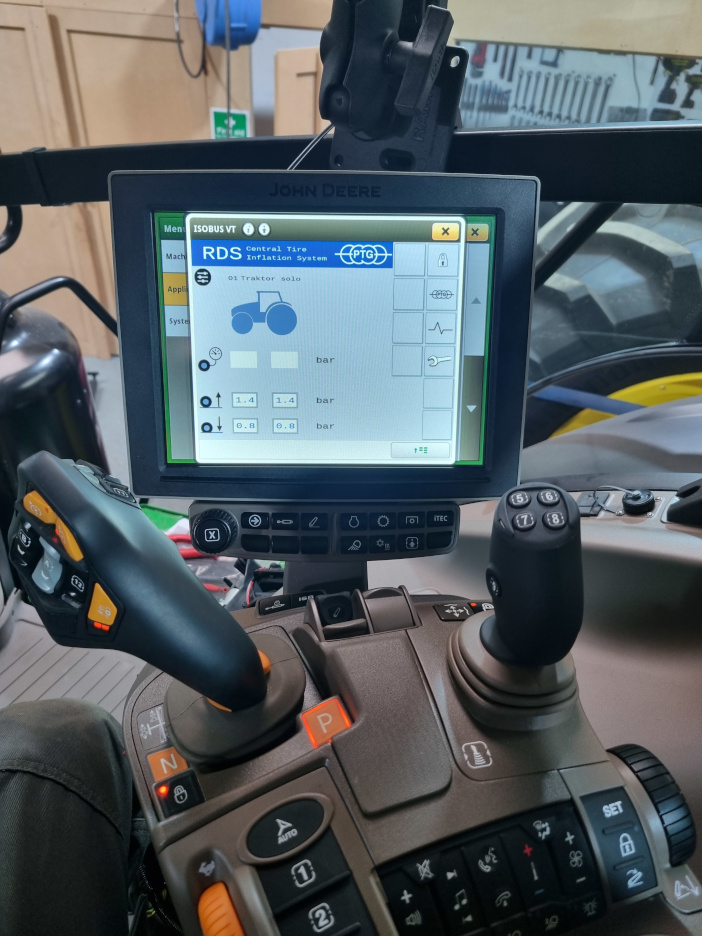
TractAir
TractAir is a UK based family business that has specialised in the design and manufacture of air brake systems for the last 30+ years. As well as supplying most major tractor manufacturers they produce aftermarket brake systems for tractors and trailers.
TractAir understood the improvements that can be gained from correct tyres pressures and saw an opportunity to use their knowledge of air systems and compressors in a new area. In 2015, they started to work alongside German specialist PTG to offer their tyre inflation systems in the UK and Ireland. PTG have 25 years of experience in tyre pressure control and is backed by its parent company Michelin.
The PTG tyre inflation system has been developed specifically for fitment to agricultural vehicles and machinery. It can be installed on any make and model of tractor, trailer, tanker, drill, harvester etc, in fact anything with wheels!
Air is typically supplied by the onboard air brake compressor. The system is controlled by the tractor screen via an ISObus interface (or a separate control unit if ISObus is not available).
The system controls airflow to the wheels using a set of valves mounted on the machine and transfers this to the wheels via rotating unions. These are mounted either in the centre of the wheels or, in the case of bar axle-equipped tractors, around the axle itself, tucking pipework away on the inside of the wheel.
A valve in the wheel rim closes automatically, ensuring that leaks don’t deflate the tyres. The pipework over the mudguards can be detached with a quick-release fitting and stored away on the mudguard. This can be helpful in particularly tight spaces but in normal use, the lines would stay attached.
Typical tractor inflation times would be 10-12 minutes from field to road, and a couple of minutes to go the other way. The ability to continue driving means that no waiting is necessary while pressures are changed.