The Contractor of the Year will be a distinguished individual renowned for their expertise and professionalism in providing advice and support to their clients; acknowledged as a vital asset to their clients’ operations and committed users of precision farming technology. The award-winning contractor will demonstrate a versatile skill set, adaptability, and responsiveness to client needs, resulting in consistently high levels of customer satisfaction.
AJ Heywood & Sons
Precision farming sits at the heart of AJ Heywood & Sons, which offers a comprehensive range of operations to customers within a 30-mile radius of its North Cornwall base. By integrating precision equipment where possible, Kevin Heywood can provide a level of accuracy and service that many of his customers would not be able to justify themselves.
He says he was the first in the area to fit the John Deere HarvestLab near-infrared system to a self-propelled forage harvester, and now runs two machines with the technology. Working alongside Ktwo Compactor push-off trailers, he can provide accurate yield mapping, with analysis of tonnage, dry matter, sugar levels, fibre and ash content, and metabolisable energy.
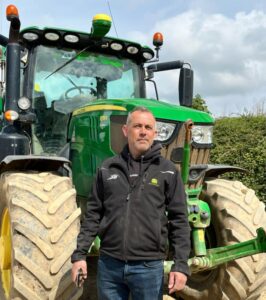
The utilisation of this equipment expanded in 2016, when it was added to the company’s slurry kit to monitor nitrogen, phosphorous and potassium levels to adjust application on the move.
According to customers, the increased use of organic manures has led to some cutting their synthetic fertiliser by half. Kevin also oversaw the construction of a mobile slurry separator, which has significantly increased the storage capacity of customers and further improve usage.
Employing precision farming technology has seen the company take on a more advisory role, and Kevin has leaned into this, putting operations manager Peter Garrad through a Basis Facts-accredited course to help customers in the future develop slurry nutrient plans from soil sampling and yield mapping results, as well as comply with environmental regulations.
JA Feed Services
With nearly three decades of experience, John Britnell runs a mobile mill-and-mix business out of Oxfordshire, servicing more than 200 farms in an area that stretches across the country from Norfolk to Wiltshire. As the sole owner/operator, he has developed close relationships with his clients, with many staying with him for decades.
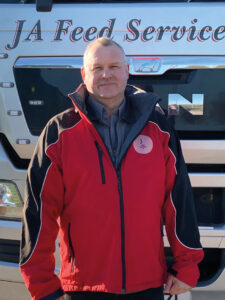
Operations are handled with an Austrian-built Tropper milling plant mounted on the back of a lorry. With a throughput of about 12t/hour when simply rolling or grinding, John can work quickly, enabling him to meet the demands of several customers in a day. The unit can also be used to create feed mixes, using proteins and minerals provided by John. A complete 4t mix can be finished in about 20 minutes.
Investment has been focused on the precision of the machine, with integrated weigh scales and a fully adjustable milling unit to meet customer requirements. To protect the health of the herd, it also features a magnet within the suction pipe to remove foreign objects.
Timeliness is key and John works with his customers to ensure that there are ample levels of feed on farm; if a farm runs out of feed, he does everything he can to get there the same day. To round out the workload, he also runs two arctic lorries to move grain between farms, and completes work for a local distillery.
NR Fell Mobile Sheep Dipping
Based in County Durham, Neil Fell set up his sheep dipping business in 2013 and treated 2,500 sheep across five farms. Just over a decade later, the business has expanded into a national enterprise with half a
million sheep dipped and units working in the Outer Hebrides and as far south as Devon and Cornwall.
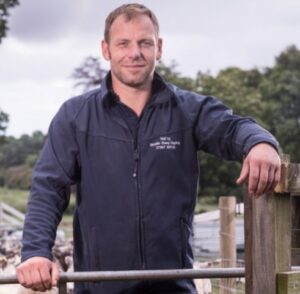
The company uses four hydraulic cage dippers, which are designed and built in-house. Neil developed the system to minimise stress on the animals and eliminate human contact with the chemicals, as well as potential spills. It has also come with efficiency benefits, more than tripling the hourly throughput of the machines from about 100 animals to 350-400.
Since developing the cage dipper in 2016, the company has been approached to help with government initiatives in Scotland and Wales to eradicate scab, and has played a role in writing new dipping codes of practice.
Last year, Neil and other staff members spent 28 days on the Hebridean islands of Lewis and Harris and completed a mass dip of 28,500 sheep to try to eliminate the parasite from the islands.
He sees his role equally as adviser and operator. New clients are met face to face and given tips on parasite control, and Neil works fast to get to clients if scab is identified in the flock. He notes that they never turn down a client, as this is not a standard operation; it is a welfare issue.