We’ve tried nearly every brand on the market,” says James Flatt. “Previously, we used a single machine to cover just over 1,800ha, but this wasn’t sustainable as we’re having to run in shifts and often work through the night.”
The choice to move to Grimme wasn’t because there was anything wrong with the previous brand, James stresses.
Instead, it came down to liking what the company could offer at the price point. “We were able to trade in one machine and come away with two six-row units for the same money it would have cost to swap like for like.”
The firm purchased a Rexor 6200, with a four-wheel chassis and a 30cu m bunker, and the larger six-wheel Rexor 6300, which boasts a 45cu m capacity.
Both are fitted with a 653hp engine, put to the ground through a hydrostatic transmission. James highlights the capabilities of the gearbox, saying that the machines had impressed him with their roading.
“We have a big job down in Harlow, which is quite a distance for us, but the Rexors handle the road really well,” he says. “They’re quiet and comfortable, and easy to drive at 40kph, which is no small feat for a machine this size.”
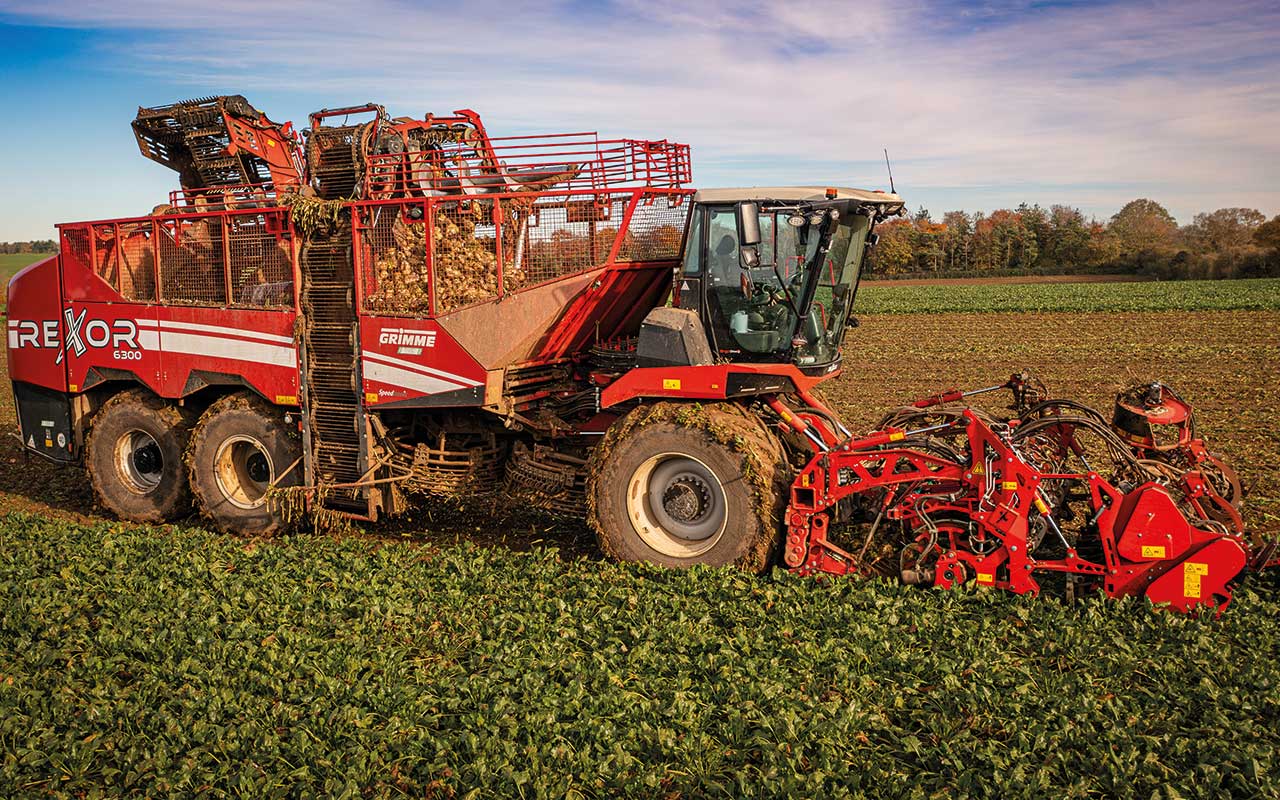
Changing at the right time
The shift in system from running one harvester to having two came at the ideal time for J Flatt.
While the decision had been made to reduce wear on the single machine, and to enable the business to handle multiple customers at the same time, in the first season they saw the hectarage increase by nearly 50%.
“There was a sudden jump in beet grown in the area, and the introduction of the early delivery scheme in 2023 meant that we gained customers,” he says.
“It means we will still be putting more than 1,000ha through each machine every season, but hopefully we can extend the replacement policy to three years.”
He also says that with a Roller Table cleaning system, they are able to travel about 1km faster than with a turbine-only setup.
“We’re working across various soil types, and in differing conditions, but the Roller Table has always been the faster way for us to get beet into the bunker.”
Increased throughput
The positive drive in the transfer web, with automatic reversing when stones are detected, is said to significantly increase the throughput as well, a point James agrees with.
He says the whole system is designed so that the operator isn’t getting in and out of the cab during work. “We can keep pushing on, which means we’re lifting more in a day.”
The only minor change he would make is the ability to rotate the driver’s seat to the left – a feature set to be introduced on 2025 models.
“This would really help as we’re emptying the bunker so many times a day. Being able to rotate through and not twist quite as much would finish the machine off.”
He concludes that while Grimme doesn’t offer a machine with more than six rows, he doesn’t believe the added lifting capacity would benefit them.
“We’ve been out to see nine- and even 12-row machines at work, but these are seriously big machines that we would struggle to get into some of our fields,” he says.
“Not only that, but increasing the size means you also need more trailers on the job, which can be difficult to source.”