The 900 range of Jaguar self-propelled forage harvesters manufactured by Claas will now benefit from a host of new features. The most significant of these is the expansion of options for the front attachment drive. In addition to the all-mechanical drive and the variable drive for the Pick Up grass and Orbis maize headers, it is now possible to equip a twin hydraulic drive, said to offer particular benefits when used with the Pick Up attachment.
Using this, the intake auger continues to be driven via the quick-release coupler and can adjust the speed in line with the length of cut. The pick-up reel features an all-new hydraulic drive which allows it to be driven with variable speed adjustment independently of the intake auger. This enables the pick-up reel speed to be automatically adjusted based on the ground speed.
This is said to provide efficient raking action at all ground speeds while reducing wear. If the ground speed or the length of cut is changed, the rotational speeds of the auger and reel are adjusted automatically. If necessary, both speeds can be adjusted to the conditions manually from the cab. The capability to respond to changing conditions manually or automatically leads to more accurate crop feeding and a more consistent crop flow.
Tests conducted in California using a Jaguar 990 and a Pick Up header showed increased throughput levels of up to 13.7% in extreme conditions when compared to the all-mechanical drive. These advantages are said to come into their own in very high yields harvested at low speeds, or low yields with a high forward speed.
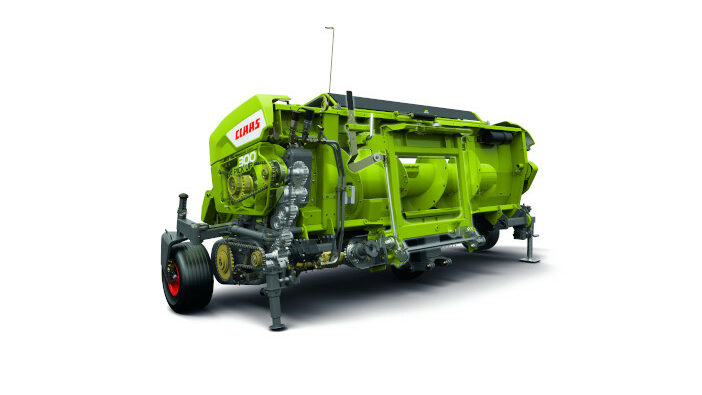
New voting for MCC Max Cracker
Claas has also introduced a new wear-resistant coating for the Multi Crop Cracker Max (MCC Max), designed to offer a fourfold increase in service life. Infield testing, MCC Max Cracker units with the BusaCLAD coating have been able to process over 3,100 hectares of maize, with some entering their fourth season.
This will not only reduce the wear costs, according to the company but also the set-up times. Operators can count on the 30 ring segments of the MCC Max to provide reliable grain and residual plant processing over several campaigns. It can work across a wide range of cut lengths and processes the crop not only with friction and crushing but also with cutting and shear force. Together these maximise the processing effect.
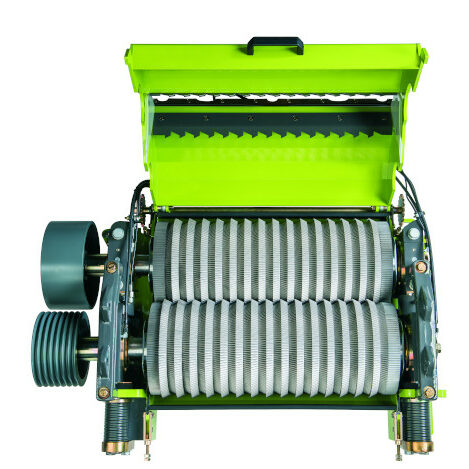
Precision dosing and water injection
As farmers and contractors increasingly use silage additives to deal with high dry matter levels in the grass harvest, Claas has developed a practical app. This will help to find the appropriate dosage and the correct set-up in line with the crop, the yield and the information provided by the silage additive manufacturer.
Key data is entered into the app to allow the correct dosage to be calculated:
- Expected yield per hectare
- Size of area to be harvested
- Working width
- Expected working speed
- Recommended dosage specified by manufacturer
- Size of additive tank
Once this has been entered, the operator can implement the recommended settings using the CEBIS terminal. They can also decide if the additive should be dosed from the Actisiler 37 tank or the large 375-litre water tank. It’s also possible to dose based on litres per tonne or litres per hectare. Data can be adjusted during work if the harvester is working faster or slower than expected for example.
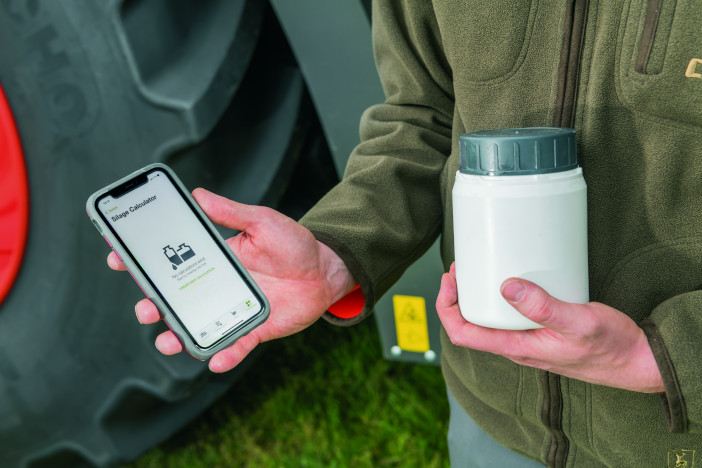
With a second, optional dosing pump, the additive injection can now be doubled, taking it to quantities of up to 800 litres per hectare. Control of the system is integrated into the CEBIS terminal. High capacity foragers can now apply additives in excess of two litres per tonne if required.
There is also a water injection system available for difficult harvesting conditions, such as in grass with high sugar content or lucerne. The system injects water into the feed unit, guide plate area and discharge chute whenever there is no crop flow – at the headland for example or during trailer changeover. This is said to help prevent the build-up of material in the crop flow and keeps the dry matter sensor or NIR sensor clean and accurate. The water tank has a 375-litre capacity and is controlled via the CEBIS terminal.
Premium Line Orbis
The company will now equip its Orbis maize headers with wear-resistant steel guide strips as standard. Previously only available as an option, the Premium Line range is enhanced with extended war coatings on existing wear parts, while other machine parts are protected against wear new, replaceable wear parts.
For more information go to www.claas.co.uk