Record global demand has led to UK manufacturer Claydon expanding its West Suffolk factory. The completion of the new purpose-built facility will more than double production capacity, according to the company, and create numerous jobs.
The expansion was supported by a £267,400 Growing Business Fund Grant from the New Anglia Local Enterprise Partnership (NALEP) and will help the 40-year-old company meet the increase in orders. Orders are expected to grow further in 2023 as the company works with distributors in export markets both new and established.
“Unlike many other companies in the UK farm machinery sector which import machinery made overseas we design, test and manufacture all our products from scratch, employ local staff and benefit the UK businesses which supply us,” said chief executive officer Jeff Claydon.
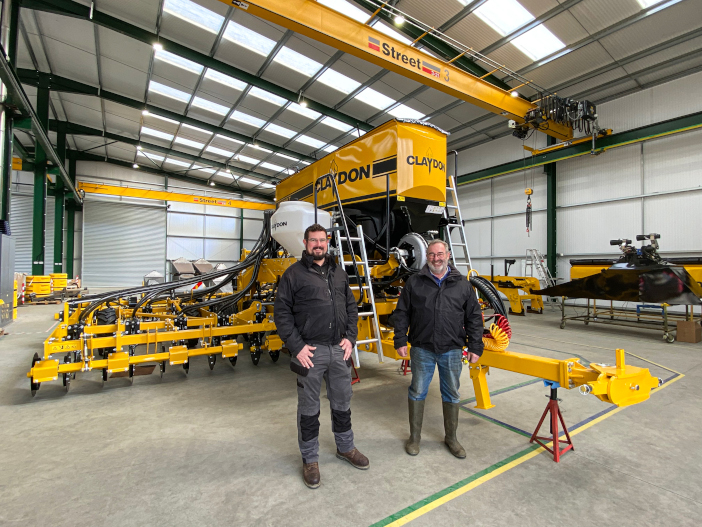
Expanding to meet demand
The company was awarded the grant in 2015, which was given out in three stages. The first stage was to construct new offices adjoining the company’s production facility, housing additional staff to support customers both in the UK and overseas.
Planning permission was granted in March 2016, and Claydon employees completed the groundworks, construction and fitting out of the building, using suppliers and contractors from across the region.
The two-storey offices blend into the existing workshop to limit the visual impact, with the top floor accommodating 27 full and part time members of staff, while the ground floor is dedicated to visitors with two meeting rooms, a dealer training and presentation studio and commercial grade catering facilities.
A £100,000 investment in solar technology provides 100kW/h of energy, reducing the site’s requirements from the National Grid and reducing the carbon footprint.
The second stage of the development, which has just been completed, involved the construction of a new assembly building, building on the footprint of derelict former farm buildings.
Mr Claydon said: “The company is growing rapidly and massively, a highly skilled team is in place, but additional production capacity is needed to manufacture Claydon Opti-Till products to fulfil demand from markets all over the world, including the UK where sales have doubled.
“Momentum is building strongly, helped by our presence at overseas trade shows, together with the ongoing expansion of our global network of importers, agents, and dealers in 22 countries, whose local knowledge and support gives potential customers the confidence to invest in UK-manufactured products.
“Despite huge uncertainties caused by Brexit and Covid-19, in July 2021 we decided to go ahead with the new building to mark the company’s 40th anniversary. Claydon staff completed the footings in the winter of 2021 and construction started in the summer of 2022. The project was managed in-house but, due to difficulties in obtaining contractors and materials, progress was slower than anticipated.”
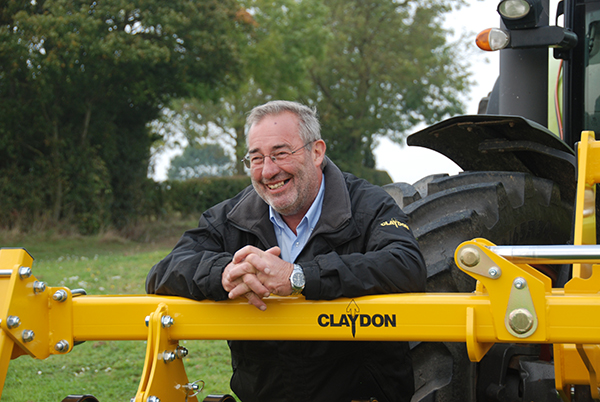
The new building measures 36mx36mx8m to the eaves, constructed from steel supplied by AJN Steelstock Ltd in Kentford and manufactured by Anglia Steel Portals Ltd at Red Lodge. The building was erected by East Anglian company S & J Fabricators, while Street Cranes in Sheffield supplied and installed the four 3.2-tonne capacity overhead cranes.
The company’s focus is now on recruiting additional staff to fill vacancies at the factory. It predicts that the requirement for assembly and yard staff will triple in 2023 and is looking to fill roles across all departments in the business.
“This significant investment we have made in these new production facilities will help us to take a quantum leap forward to meet demand for Claydon products and is a key part of our long-term plan to develop the potential which exists all over the world,” Mr Claydon concluded.