Heinz-Günter Gerighausen, Chamber of Agriculture North Rhine-Westphalia, Kleve Technical College, Kürten
Quality assurance has a very high priority in forage harvesting. From mowing to storage, all concepts are aimed at gentle handling of the soil, low-loss cultivation in the field and fermentation that is reliable in terms of utilisation. Combinations of several mowers offer the possibilities of ‘controlled-traffic farming’ for the first time. The new-generation belt windrowers offer more than just effectiveness, and the recovery system allows the targeted use of silage additives in all harvest chains. And in the case of baling presses, the use of new sensors ensures automatic workflows with the same bale quality.
Silage preparation
Performance-oriented feeding of ruminant animals requires an optimal fermentation process with high fermentation stability. The natural environmental conditions do not always allow this type of silage process. Then silage additives on a biological and/or chemical basis are required. The industry offers a wide range of currently necessary and supporting active ingredients. It is now up to the entrepreneur and service provider which active ingredient is used in which concentration. Both parties involved, the farmer and the forage harvester or loader wagon driver, have other important tasks to perform in addition to mowing, tedding and swathing, so the decision on the selection and quantity of the appropriate silage additive is usually neglected. A new app now offers a consulting tool. This app helps both the farmer and the forage harvester driver to mix the right amount of silage additive for the set harvest target and to apply it correctly. As a result, it is already clear at the beginning of the application what quantity is needed, which avoids overdosing or underdosing. As several application points are possible in the chopper (in the area of the drum, the accelerator or the tower), an indication of this is also available in addition to the choice of active ingredient – quality-assuring support in the right direction.
What is already standard in the chopper should also be an option for the other recovery equipment. Of course, there are already enough dosing devices that are primarily time-controlled.
Newer systems have an additional operating mode in which the dosing rate is controlled by the throughput. For this purpose, the weighing chute (alternatively an entered weight) is used in the pack press. A fixed rate (l/t) can be selected here, or an automatically adjusted regulation (l/t) can be made depending on the humidity. It should also be possible to use this type of metering ‘tomorrow’ in the loader wagon and the round baler. Then the secured fermentation process will be perfected.
Mowers
Every Agritechnica offers the opportunity to show innovations or further developments. Manufacturers use them especially in the area of mowing technologies. Slope-controlled mowers are nothing new; we saw the technical solutions for rear-mounted mowers at the last trade fair. These are interesting developments, but they put the ‘cart before the horse’. When cornering or on slopes, the overcut of the 3-metre front mowers is not sufficient to avoid drossing. However, this swathe is flattened by the rear wheel before the cut-adapted rear mower has been able to mow this strip. Therefore, the clear specification: either wider folding or hydraulically controlled and movable front mowers. There are an increasing number of these solutions, and all of them are clearly headed in the right direction. If the steering angle of the front axle is also used for steering, all the better.

In arable farming, driving lanes are a matter of course. They are still unknown in grassland and forage production. However, ‘controlled-traffic farming’ is increasingly an option in large-scale field forage cultivation, especially in combination with legumes. In the case of multiple cuts and consequently passes, lucerne and certain types of clover particularly suffer. Fixed working widths of around 12 metres with a single ‘working track’ only make sense, however, if only this one fixed track is used from fertilisation to harvesting. Apart from mowing, all other areas are effectively covered and therefore technically well solved. There was just no suitable solution for mowing with swath placement. With a coupling frame in the three-point for two trailed mowers, the utilisation of powerful tractors with commercially available front and trailed mowers is possible. Working widths of 12 metres and more are possible, as is the continued use of the individual mower units. This is an innovation for large-scale cultivation with the special aspect of soil protection in the non-overrun area.
Windrower and bale wrapper
Some farmers and contractors have solved their solutions for the combination of swathing and bale pressing and wrapping in an energy and soil-saving way: reel or beam windrowers were primarily used for swath formation. Now we have a development directly from the manufacturer in combination with a roundabout windrower. With intelligent control/automation of the roundabout windrower, the pick-up of the baler lifts out with a time delay. The windrower lifts out the rotors and, if desired, also the pick-up when net binding starts on the round baler. In addition, a large number of individual hydraulic functions can be carried out manually. The major test is still to come for this first solution that complies with the German Road Traffic Licensing Regulations (StVZO).
Belt windrowers are not a new achievement. The further developments in detail show the importance of this technology in forage-friendly harvesting. They are not cheap but inexpensive, not light but powerful and versatile. ‘Global players’ also recognise this and have bought into Europe. It is the ‘windrowing system’ with the most diverse variants and areas of application. Smaller working widths in the front attachment offer the possibility of even swath division for the centre windrower trailing in the rear. The aim is not to drive over the forage and to build up an even swath for the following harvest chain. The same objective is pursued by the solution for tractors with reverse drive equipment. Whether a centre or side swath is concerned, all variants are possible without driving over the forage.
Loader wagon
Short chop lengths for silage offer some advantages, for example higher density, better removal or better breakdown in the feed mixer. The 35 mm cut on the loader wagon is standard. Shorter cutting lengths have been around before. The Danish company Taarup had a loader wagon in its product range with a 74-blade cutting unit and a 20-mm cut, divided into 6 hydraulically secured holding blocks. The high-power requirement was the reason for a reduction to 37 blades in the 1980s. Today, with drive power no longer the limiting factor, 65 knives with a 25mm cut in the loader wagon cutting unit can almost compete with the chopper. The biggest shortcoming in this comparison: the removal and sharpening of the knives is much more time-consuming. It is also important to bear in mind that this very expensive loader wagon requires more effort for transport than for loading and unloading. This can be a disadvantage in direct cost comparison with the chopper.
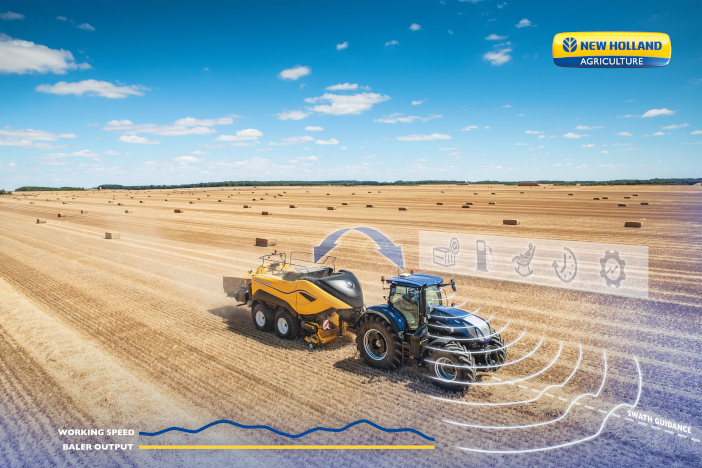
Pressing
Big balers are mainly used for hay and straw harvesting. More than 90% of the bales are still set down individually. And this despite the fact that there are directly attached ball collecting wagons in various designs and sizes. The use of this technology is more than effective and necessary, as it considerably reduces the amount of driving and with it the tracks in the field. Nevertheless, it is surprising that the purpose of this technology does not really seem to have arrived in practice yet. Is the use of tractors, wheel loaders and telescopic handlers so much cheaper, better, and more efficient? Even if the bale collection trucks can form so-called bale lines automatically controlled by GPS. This is a great development that is worth exploring in greater depth, both theoretically and economically.
The equipment of the modern large-capacity balers leaves almost nothing to be desired. Bale dimensions and bale densities as desired are no trick. Stable binding at high throughputs and densities is also guaranteed. What remains unresolved is the uniform set density in the bale at any time of the day, with every field change and also when cornering.
Drivers are continuously challenged during pressing. They have to keep a constant eye on the swath in front of them so that, on the one hand, all of the crop is picked up and the bale chamber is filled evenly, but on the other hand, no disturbances or even blockages occur. With the ‘big bale automation’ we now have the first system where the driver can directly set the desired bale weight on an agricultural square baler and the system then anticipates and automatically takes over the machine guidance as well as the regulation of the tractor speed and the baler settings. A special sensor optically measures the swath in front of the tractor using a laser, while another sensor controls the acceleration and orientation of the tractor. For even greater accuracy, the information from the tractor’s GPS sensor is also processed. In this way, the tractor is guided over the swath fully automatically and the speed is adapted in advance to the swath conditions. At the same time, the recorded data is used to continuously calculate the bale weight in advance in order to adjust the setting of the baling pressure and the layer thickness of the individual piston strokes via the driving speed. This ensures that the baler is continuously utilised even under changing harvest and yield conditions and that the same pre-set bale weight is always achieved.
This automation relieves the driver on long harvesting days and helps to keep the balers running at high productivity levels even on dusty days and in the dark. A uniform bale weight facilitates the planning of subsequent logistics. Even though many individual aspects of the system are known, it is a holistic solution with great practical benefits.
Conclusion
Software alone does not determine further developments or even innovations. A good balance of the different hardware and software components is of increasing importance in practical use. Because proven technology is gladly subjected to the necessary daily maintenance and care, which we are proficient in. Manufacturers and developers have recognised this, and today it is the basis for the technology of tomorrow.