The German Agricultural Society (DLG) has announced the winners of its innovation awards, ahead of Agritechnica which will take place from February 27th to March 5th, 2022.
The awards are open to any exhibitor at the event and this year there were 164 submissions. The DLG Innovation Commission examined each entry during a period of consultation and deliberation before narrowing down the field to one gold medal winner and 16 silver medal winners.
The criteria for a gold medal winner is that it is a new concept or changed functionality that has a tangible relevance at the farm level, with benefits to profitability and processes, the environment and energy use, or to workload and operator safety.
Silver medal winners should be innovations that have been enhanced to such an extent that there is a substantial improvement to functions and processes. This too should have a tangible relevance at a farm level, as well as benefits to workload and work quality, or improved reliability.
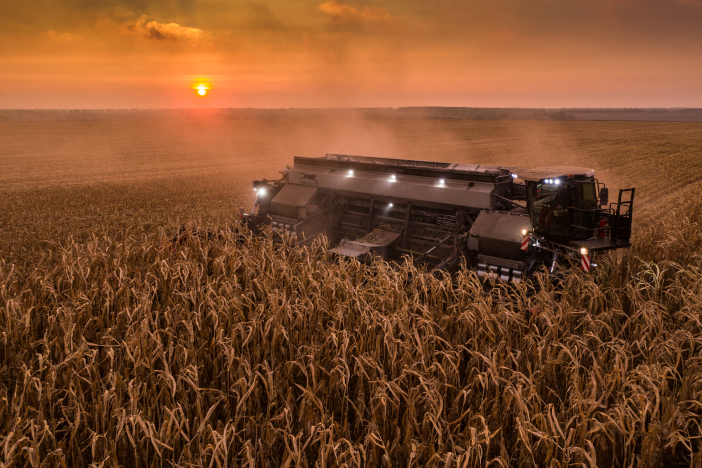
Gold medal winner – NeXaT-Systemtraktor
The NeXaT is a carrier vehicle that can be used for crop production work, from tillage and sowing to crop protection and harvesting. Implements are carried on the machine, which is said to significantly increase efficiency, with the 12m wide model tracking over just 5% of the field.
It’s designed as an autonomous working machine and is equipped with a monitoring system, but can be manually operated for transport. Integrated implements are mounted between the four electrically driven wheels, which rotate 90 degrees to switch between fieldwork and transport. Power is supplied by two diesel engines, each offering 545hp, with generators. The manufacturer suggests that it is also designed for alternative fuel technologies.
When equipped with the NexCo combine harvester module, the NeXaT can reportedly achieve throughputs of 130 tonnes to 200 tonnes per hour. It uses a 5.8m long axial rotor which divides the product into two material flows. Grain delivery comes via a 32 cubic metre bunker, large enough to ensure that emptying take can take place on the headlands in most fields. Unloading capacity maxes out at 600 litres per second, meaning the bunker can be fully emptied in just one minute.
Silver medal winners

AGCO (Fendt) – Automatic dust extraction system
Fendt has introduced a new automatic system that monitors how dirty the air filter is. When a predetermined level is reached, two powerful pressure pulses loosen the dust on the filter. This is then sucked out of the housing using a vacuum, produced upstream of the hydrostatic cooling fan.
The system is said to eliminate manual cleaning of the air filter and can be actioned even when the tractor is under full load. Downtime can therefore be reduced, alongside fuel consumption and maintenance.
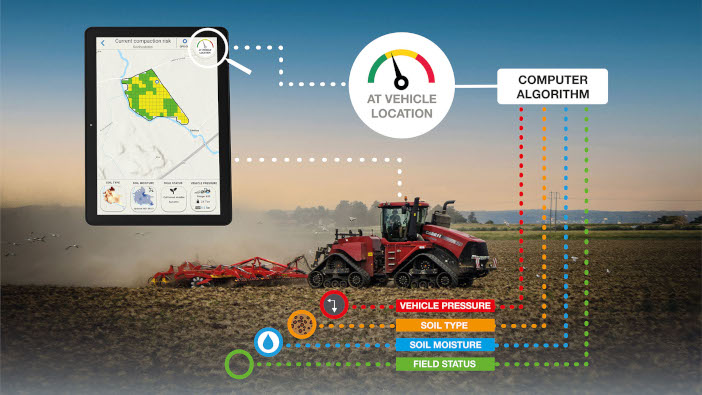
Agtech 2030 – Compaction Prevention System (CPS)
The CPS system from AgTech 2030 shows the current compaction risk for the field in the form of a map. The location-specific calculation is said to help the operator to plan work, as well as possibly avoid certain at-risk areas in the field. Including in the calculation is variable statuses, including tillage method, the crop and level of vegetation.
It offers decision making aids to the operator, potentially eliminating compaction alleviating tillage operations as well as reducing emissions.
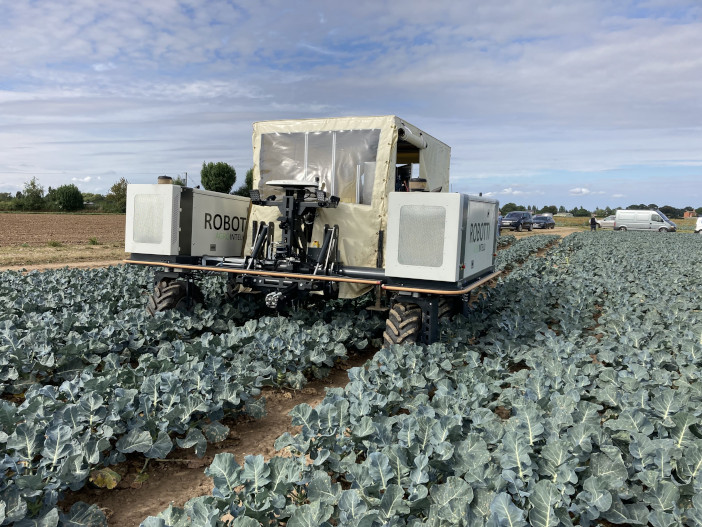
Agro Intelligence ApS (joint development with RoboVeg Ltd) – RoboVeg Robotti
An autonomous robot for selective broccoli harvesting, the RoboVeg Robotti combines an Agro Intelligence field robot with the broccoli harvesting robot from RoboVeg. It has two engines for a combined output of 104kW, a lifting mechanism that can hold 750kg, and comes equipped with high-resolution 2D cameras and 3D sensors.
Two robotic arms swivel around six axes to pick the crop, reportedly taking just three seconds from selecting the plant to putting it down. Harvesting performance is said to be around 2,400 plants per hour, compared to 300-360 plants during manual harvesting.
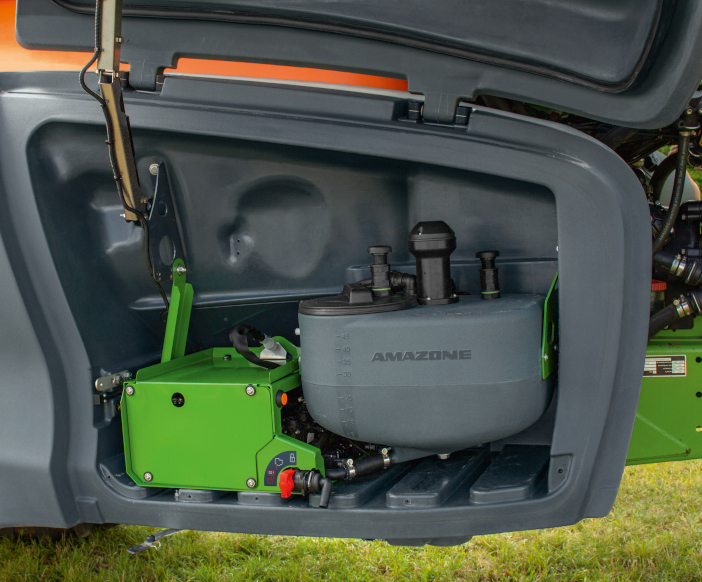
Amazone – DirectInject system
An integrated direct injection system available on the company’s range of sprayers, Amazone DirectInject can apply concentrated crop protection chemicals where required. It can handle both liquid and granulated products, with the unused products returned to the container so that the required amount does not need to be known ahead of the operation.
As the system is integrated, it can be used accurately with application maps, as well as been controlled via the ISOBUS system with automatic cleaning via the Comfort-Pack plus. Using the system, additional passes are eliminated, saving fuel and protecting the soil.
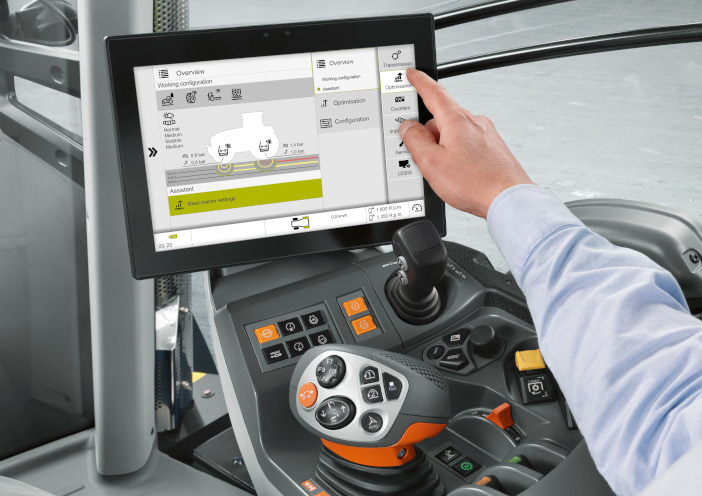
Claas – Terranimo
Displayed on the in-cab terminal, Claas has developed a system to warn operators of the risk of compaction. To calculate this, it uses information from the CEMOS driver assistance system, including soil type and condition, axle loads and tyre pressures. Terranimo then simulates soil loading, including dynamic axle loads, and indicates areas at a high risk of compaction. The operator can then choose to abandon the operation or make adjustments to ballasting or tyre pressures to alleviate the issue.
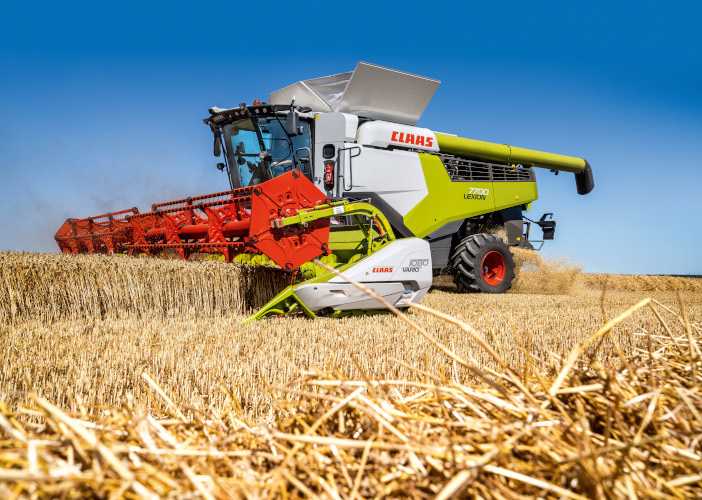
Claas – CEMOS auto header
Claas has adapted its CEMOS driver assistance system to offer automatic adjustment of auger cutter bars for its range of combine harvesters. A laser scanner registers the height of the crop and the operator specifies the nominal immersion depth of the reel into the crop and the horizontal position. These are then automatically adjusted as the crop height changes.
The system can recognise tramlines and the end of the crop, as well as adjust the length of the table to ensure a consistent crop flow. Using the system, Claas states that maximum output can be achieved.
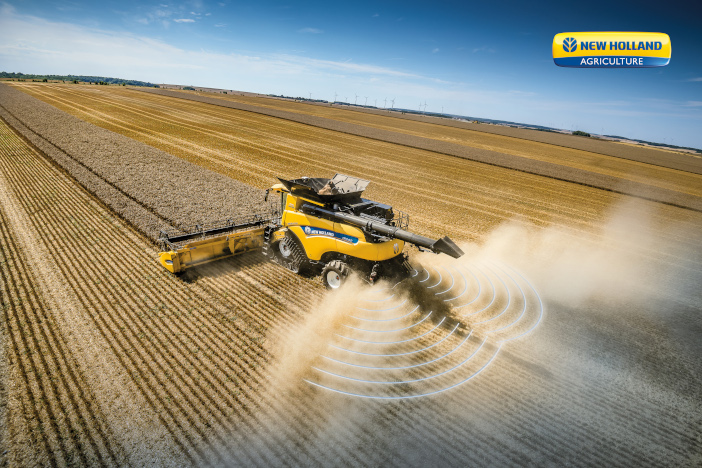
CNH Industrial (New Holland) – OptiSpread Automation System
To ensure the uniform distribution of chopped material behind the combine, New Holland has developed the OptiSpread Automation System. It uses 2D radar sensors, mounted on both sides of the harvester, to measure the speed and throw of the chopped material. If the distribution pattern differs from the norm, the rotational speed of each rotor is adjusted to fix this.
It can register any irregular distribution caused by wind conditions for example, and produce a distribution map at the end of the operation.
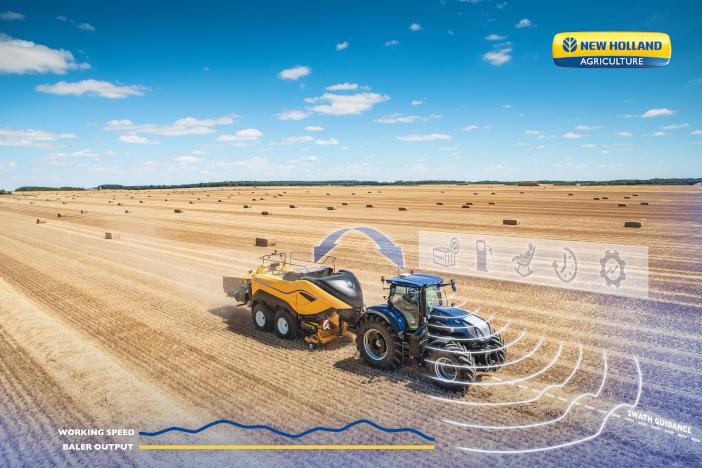
CNH Industrial (New Holland) – Big Baler automation
Reportedly the first system of its kind, New Holland’s Big Baler automation enables the operator to set the desired bale weight, after which the machine takes over machine guidance and regulation of tractor speed and baler settings to maintain this. A LiDAR sensor (Light Detection and Ranging) measures the row head, while an IMU sensor detects acceleration and orientation.
Information from the GPS sensor is additionally processed to achieve even greater accuracy. The data is collated to pre-calculate the bale weight and adjust pressure settings and forward speed, ensuring that the machine is at maximum capacity and producing consistent bales.
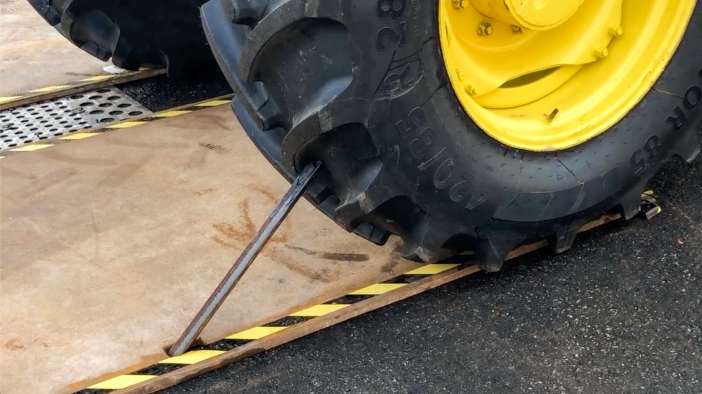
Continental – Agro ContiSeal
To reduce the risk of blowouts and minimise downtime by allowing the operation to continue even when a puncture occurs, Continental has developed the Agro ContiSeal. A viscous polymer on the inner side of the tyre seals the hole. This not only enables the operation to be completed, but it can also help operators avoid tyre changes or repairs during tight time windows or in difficult conditions.
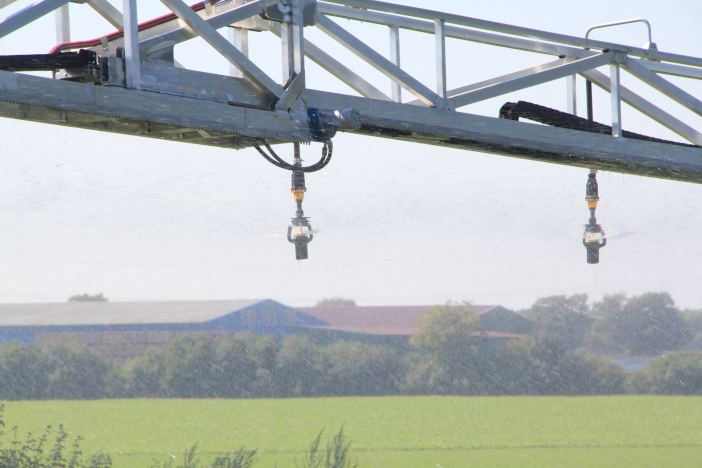
Fasterholt Maskinfabrik A/S – DL 66 Pro
The DL 66 Pro is a combination of a mobile irrigation machine and a mounted nozzle carriage, consisting of a telescopic and hydraulically folding 66m boom. It enables operators to benefit from the low pressure, efficient irrigation capabilities of a nozzle carriage, while also using up to 1,000m of piping and moving up the bed thanks to the mobile irrigation system.
It’s divided into 10 sections, each with its own water supply, making section control possible in the future. With this system, it is possible to irrigate up to eight hectares in one machine setup. The hydraulic actuation of the telescope and the folding mechanism also means that one operator can reposition the machine.
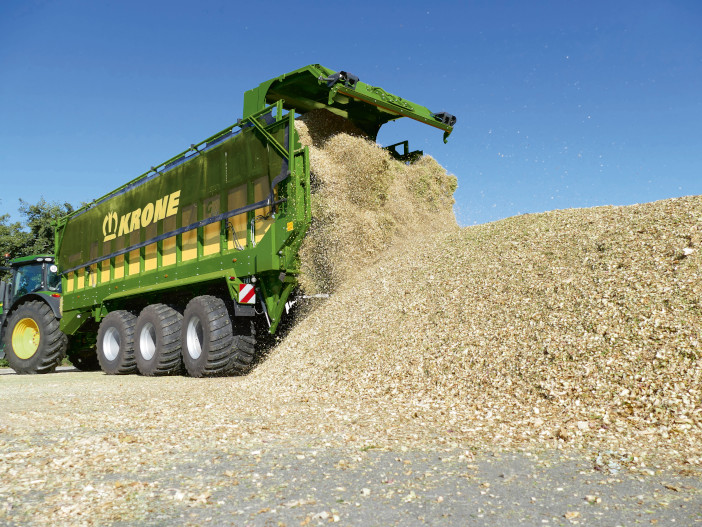
Krone – ExactUnload
Available on the latest GX loader wagon, Krone has developed ExactUnload, which can automatically adjust the distribution of material in the silage pit. Using the roller bed floor and the moving front wall, the machine measures forward speeds up to 3.5kph and the length of the pit to adjust the unloading speed.
This is said to offer increased operator comfort and more consistent compaction and distribution of silage. It also minimises driver errors and saves fuel and time.
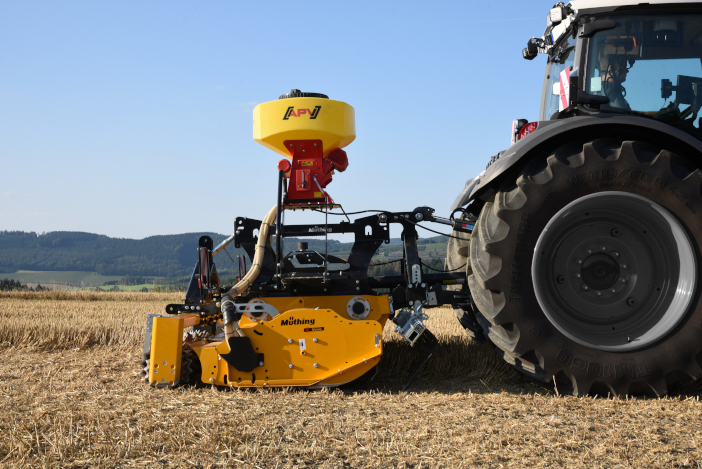
Müthing – CoverSeeder
Combining residue management and direct drilling for the convenient establishment of companion crops, the CoverSeeder from Müthing is said to improve accuracy, when compared to broadcasting seed, as well as reducing passes.
It comprises a front-mounted harrow to create a tilth and distribute crop residues. A trailed flail mulcher shreds the residue and stubble and uses suction power to remove it from the seedbed. The mixture is conveyed over the seed rail, which places grain on the exposed bed and placed over the seed. The following prism roller ensures good soil contact. A key advantage is said to be the preservation of moisture, vital in dry conditions.
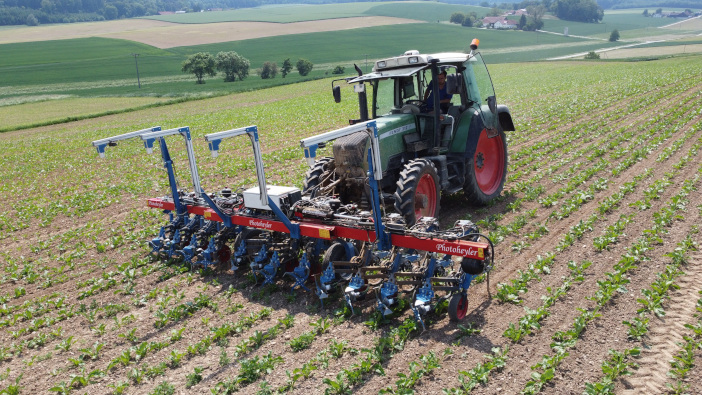
Planungsbüro Heinrich – Photoheyler
Featuring a rotor concept for outputs of more than one hectare per hour, the Photoheyler mechanical weeder features camera-aided row guidance and hydraulic steering cylinders which are synchronised with the tractor. Due to the position of the rotors, the cutting angle is always 90 degrees to the crop, cutting weeds out of the row and placing them in the path of the trailing tools. Various tool combinations are available to suit operations.
It’s also possible to combine the machine with a seedbox, placing the seed in a delta configuration across the entire width of the machine. The company also states that spot spraying applications will be available in the future.
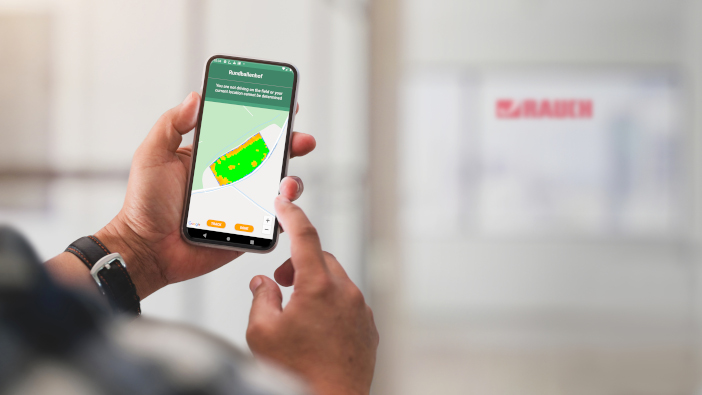
Rauch Landmaschinenfabrik GmbH (joint development with AgriCircle AG) – TerraService
A digital service jointly developed by Rauch and AgriCircle AG, TerraService calculates the navigability of arable land ahead of operations. Users input machine data for the task and soil moisture levels are estimated using satellite information and weather data. The system calculates the navigability and can break the field down into 10m grids.
If necessary, the system can provide a warning if there are potential for significant soil damage or difficulties. The system can be adjusted to suit different tasks, including fertilisation, slurry application and crop protection.
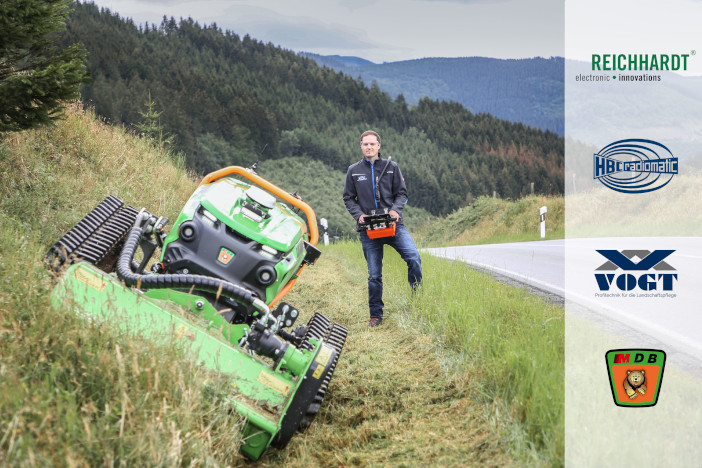
Reichhardt GmbH (jointly developed with HBC-radiomatic/Vogt GmbH/MDB s.r.l) – SIS Remote
The SIS Remote is an integrated control system for remotely controlling autonomous agricultural machinery. It consists of a radio control system and ISOBUS functionality and can be scaled to meet the demands of tool carriers. The system can be combined with GNSS navigation and RTK signals to fully automated operation, while still protecting the operator in high-risk areas.
It was initially developed for landscape management but meets all the requirements for autonomous operation.
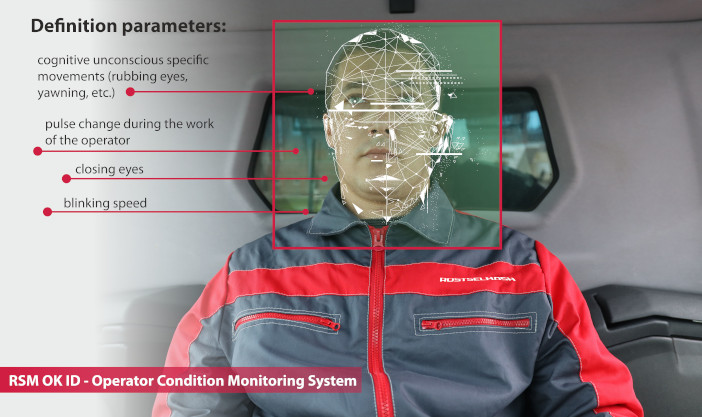
Rostselmash – RSM Ok ID
The ramifications of an operator falling asleep at the wheel can be very serious and are a real risk during the long days and monotonous tasks involved in agriculture. The RSM Ok ID system intelligently monitors the driver’s state and notifies the operator if it detects drowsiness or other changes of state.
Pupils, blinking, head position and pulse are monitored via a camera. As it is linked to the machine’s ISOBUS system, it can stop the machine to avoid potential accidents. It also generates a message to the Agrotronic farm management system.