For many, it will not be the moisture that causes headaches at harvest, but the prevalence of weeds in the crop.
John McArthur, managing director of McArthur BDC, explains that the ability to clean crops will be more important than ever.
See also: Scottish grain handling demos prove a huge success
“It isn’t just dirty crops that will benefit from this, although there are stricter specifications than ever for clean seed,” he says.
“We’re seeing wider rotations and more farmers looking at multicropping, so being able to separate multiple species and remove impurities could bring about a lot of opportunities.”
These opportunities extend to contractors, for whom there are various mobile processing units available from McArthur.
The JK Machinery VibroCompact can be mounted on a trailer with its own power source and offers a throughput of up of 15t/hour when doing a general pre-clean and 5t/hour on a detailed cycle.
The company also retails the Kongskilde KDC rotary cleaner as a trailer mounted unit, with throughputs reaching 40t/hour even when working to exact specifications.
“Contractors could easily see a quick return on investment as premiums become more vital than ever for growers,” John notes.
“And those same farmers will look to contractors as a more cost-effective way of ensuring a clean crop than redesigning and installing new systems.”
Clean and dry grain
Tornum director Charles White also notes the importance of cleaning crops, even if weed pressure has not been an issue. “Running the grain through a cleaning unit, even quickly, will help remove a lot of the chaff.”
He says decisions about grain after it is off the field is a balancing act, one that needs to be based on the crop grown and the premium targeted.
“As an example, for malting barley you would look at the quality over the moisture.”
Charles adds that technology is making these decisions easier for growers, with optical sorting systems helping to remove infected grains, weed seeds and other crops from the processing unit by using an infrared camera.
“Our Intelligent Dryer Control has also proven to be popular, with nearly all new dryers having the system, as it enables growers to accurately dry their crops to a target.”
He says overdrying can be a costly mistake for growers. If you take a standard drying operation, bringing grain down from 15% to 14%, Charles explains that the cost of drying increases as the moisture content gets lower.
“It’s easier to remove the moisture at a higher percentage. Once you get below 15% it becomes more difficult and takes longer.
“Overdrying by just 1% to 13% could increase costs by 30%. Leaving it in the dryer until it is at 12% would increase costs by 50%. That’s without considering the lost income due to the weight reduction.”
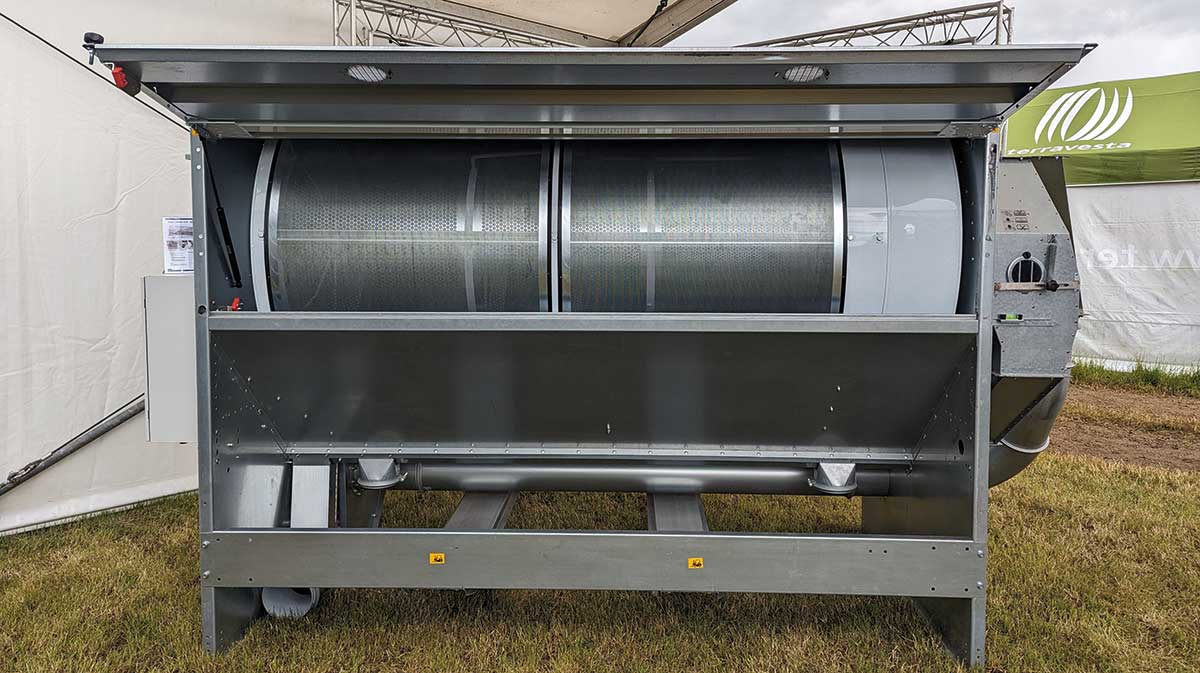
Automating the process
The benefits of automation are greater than growers think, explains David Perry, managing director of Perrys of Oakley.
“Firstly, there is the ability to leave a dryer and plant operating on its own, while having the peace of mind that the grain moisture content incoming and outgoing is being accurately sampled and the dryer discharge speed is being controlled to maintain the output moisture content as accurately as possible.
“We calculate that by combining hot air recirculation, insulation and automatic moisture control, the operational dryer cost savings could be as high as 35%.”
He adds that growers are paying more attention to cleaning and processing equipment, either updating old models with moisture sampling and automated control, or planning new stores.
If growers are caught out this year, having to run greater amounts of grain through the dryer and putting pressure on the capacity, David says they shouldn’t worry too much.
“We would recommend that growers plan for average conditions, not the worst case. This is where automation really helps because the dryer can run for 24 hours, providing flexibility to handle any additional tonnage.”
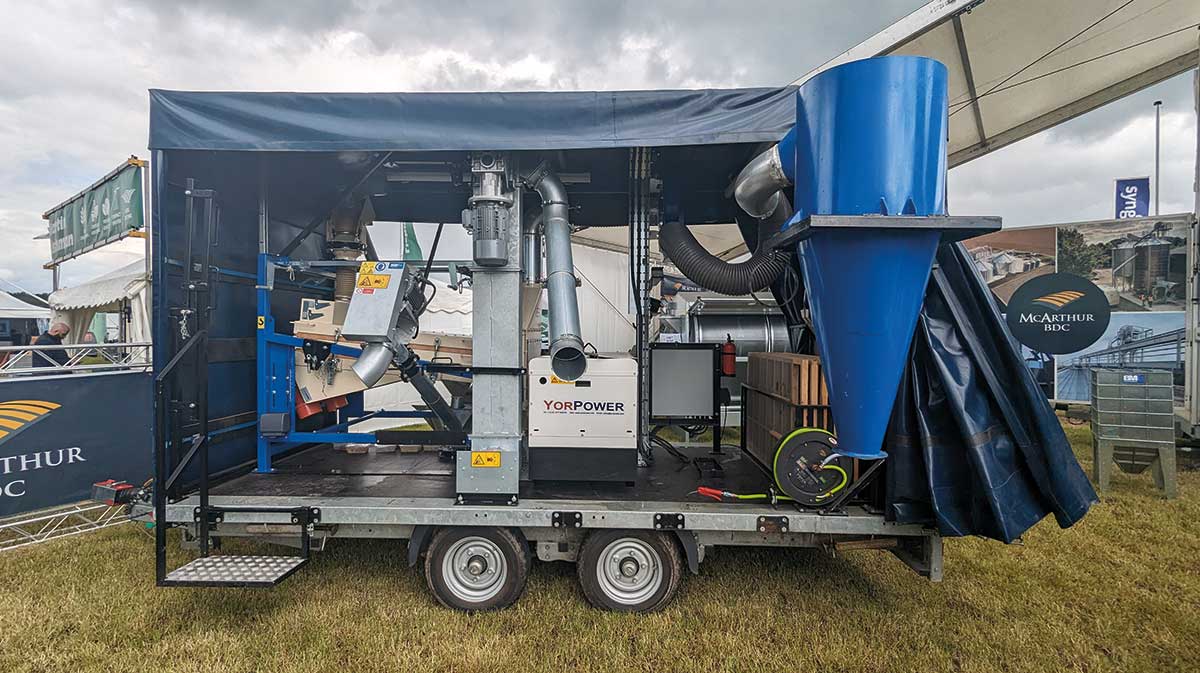
The cooldown
According to Joel Capper, managing director of Martin Lishman, the cooling process needs just as much consideration as the drying process.
“Heat causes spoilage,” he says. “Growers put so much time and effort into producing a crop, they should take every measure to not let it be ruined at the last hurdle.”
Storing grain at a higher temperature causes the heat to interact with the remaining moisture. This can lead to infestations in the crop, as well as mould.
However, Joel believes more people are looking at cooling, with increased interest in the company’s cooling pedestals, capable of work in grain stores up to 18m deep, with throughputs of up to 1,000t per unit.
“We offer four different sizes of pedestal to suit the setup of each grower,” he adds. “These can be used
to target hotspots within the crop, either directly out of the combine, or from the dryer.”
Cost-effective cooling
Joel says cooling isn’t just a vital part of ensuring that grain is of the best possible quality, it can also be a cost-effective way of conditioning grain that is hovering near the correct moisture.
“Combined with automation for controlling the climate in the store, correct cooling can remove upwards of 2% moisture from the crop. This means growers can get their grain to the correct moisture at a reduced cost, if needed.”
Evans and Pearce managing director Rob White agrees that cooling is a vital part of the grain-handling process – one that can sometimes be overlooked.
“If you look at the AHDB recommendations, based on 1,000t, you should have about 6cf/min of airflow running through one tonne of grain to ensure rapid cooling and avoid spoilage. If you look at what we offer, a system will cost in the region of £4.5/t and would last the grower between 10 and 15 years.”
He adds that reducing fan numbers to save on the upfront costs would only save about 60p/t of grain, but reduce the cooling capacity by about 25%. This leads to a greater risk of spoilage.
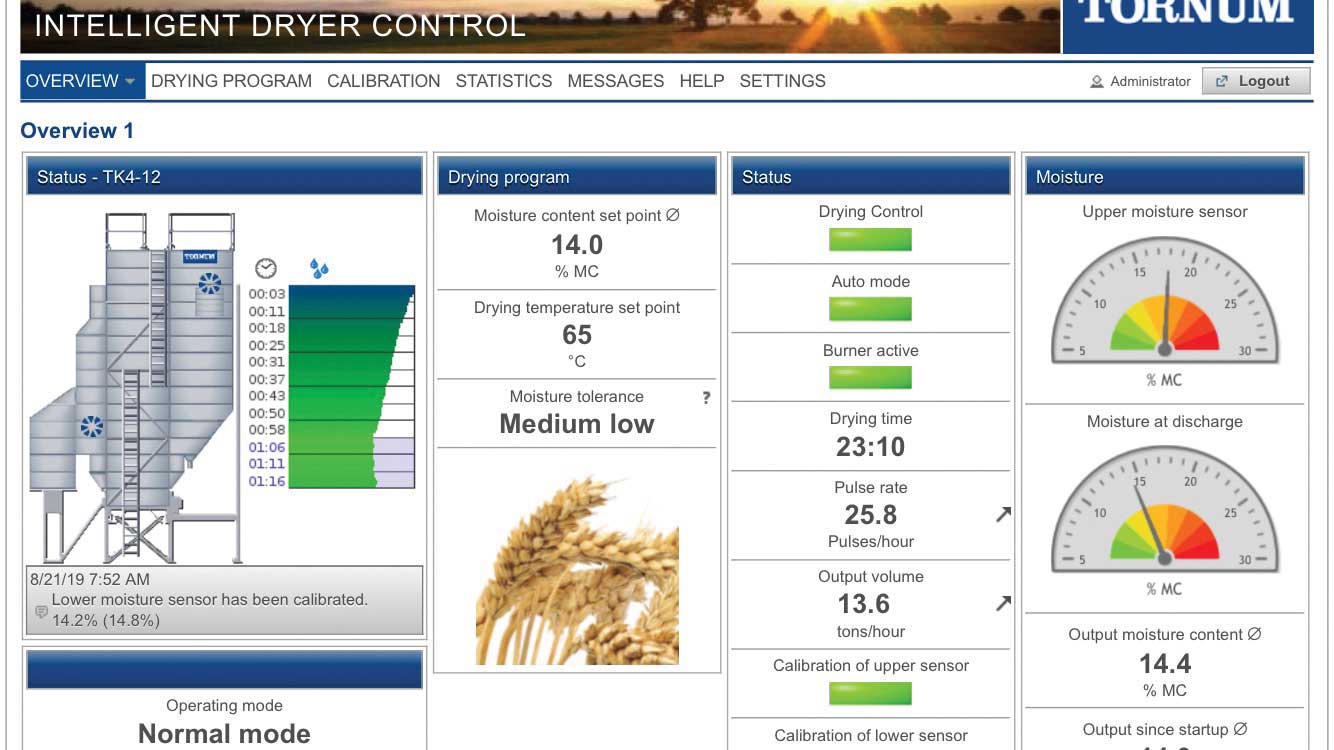
Plan ahead
He recommends forward planning when it comes to grain handling by either maintaining old systems and keeping a supply of spare parts, or carefully looking at the requirements when installing new processing units.
“I’d always recommend a differential temperature control. Costs have gone up and unnecessary running times and poorly stored crops can be a financial drain.
“You can’t control what you don’t monitor, so these systems pay for themselves very quickly,” he says.
He also highlights the importance of screening seed samples this year for growers who are looking to use farm-saved seeds.
“It’s likely that certified seed will be in short supply, so more growers will be looking to save their own,” he says.
“This comes with its own risks, so growers should prioritise quality and screen samples because of the prevalence of diseases such as fusarium, as well as nuisance weeds.
“Independent trials by SGS have shown advantages to grading seed and removing the low weight fraction.”