At the Frameless art exhibition in central London, Hutchinsons laid out its plan for the next phase of the Omnia farm management system
In hindsight, Frameless was the ideal location for Hutchinsons’ product launch. In the same way that the exhibition aims to fully immerse visitors into its art pieces, the latest updates to the
Omnia system are designed to immerse growers into every aspect of their business.
The Omnia system has been on the market for eight years, initially used as a precision mapping tool and now comprising various modules to monitor yield, crop rotations, cost of production and carbon mapping tools.
A series of updates are now being integrated into the Omnia system. It is designed to ‘connect the dots for British farmers’, according to managing director Gordon Mckechnie, enabling them to produce more from a reduced area of arable land, as ground is put into environmental schemes or otherwise taken out of production due to sales or diversification.
“This will be the most advanced, easy-to-use farm management system on the market,” he said. “It will allow users to optimise their production and minimise the use of inputs. It is a shift in the way agriculture is practised.”
Spray plan module
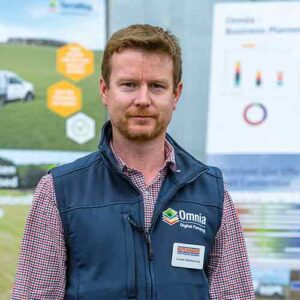
According to Lewis McKerrow, digital farming manager, the new spray plan module has been one of the most requested features from customers. “Despite changing legislation around the use of actives, there has been very little innovation in this area,” he explained.
Using a combination of existing and user-provided data within the system, customers will now be able to create spray plans in Omnia, which are then checked against application information and crop suitability data contained within Hutchinsons’ bespoke HALO database.
“As the spray plan is inputted, it will undergo a series of basic checks instantly,” Lewis added. “This will include whether the right product is being applied to the correct crop, if the date of application is in line with regulatory and product approval rules, and if the crop growth stage and application rate are within the acceptable limits.”
If the instant checks come back without any issues, users can run the spray plan through the HALO module, which conducts a digital audit, ticking off 15 criteria to ensure that the spray plan meets the regulatory requirements. Using historical data within the Omnia platform, it can also monitor the active loading on a field across multiple years, ensuring that users do not inadvertently overapply across a crop rotation.
“This has been a massive project for Hutchinsons,” Lewis continued. “Using core data from the Food and Environment Research Agency, alongside daily industry updates and information from our own agronomists, we have structured nearly 50,000 data points for inclusion in the system.”
The system also advices on tank mix sequencing, automatically sorting products into the correct order on the dashboard and the mobile application to limit the risk of human error. This function is on by default, but can be switched off to allow the grower to sequence the mix if required.
Data is wirelessly transferred to the mobile application, meaning that the sprayer operator can access it whenever it is required. Built into the app, a tank mix calculator helps to accurately measure out actives and water volume for each field.
While the system is designed to enable growers to run a paperless business, if required the spray plans can be exported as a PDF and printed to show to a contractor or worker who does not have access to the app.
Task scheduler
Bringing the Omnia system in line with other farm management systems is the updated field diary module, allowing tasks to be scheduled, sent to operators and recorded while in process.
Previously, the system had been able to record field inspections, but not in-field operations.
Access to the system is split into three levels, with the task manager accessible to office staff and the farm manager, task data available to operators and agronomists, as well as managers, and the record function being available to all the above and inspectors or auditors.
Using the task manager functionality, tasks can be created, assigned to an operator, machine and field, and scheduled on the calendar. This task is then synced with the mobile app, meaning workers can see the details and timeliness of operations.
If an operator is due to cover multiple fields in a similar area (for drilling or spraying, as an example) these tasks can be combined into a single, scheduled job.
Finally, the record function means the office and farm manager can be updated in real time when jobs are started and completed. The maps within Omnia are automatically updated when tasks are completed, and notes can be added to inform growers of any issues or points of interest during the task.
As with the previous functionality, this module can be linked to other manufacturer-led systems and can be accessed through any device. Data from the field diary is also fed into the production module of Omnia, allowing the gross margin analysis to be kept up to date.
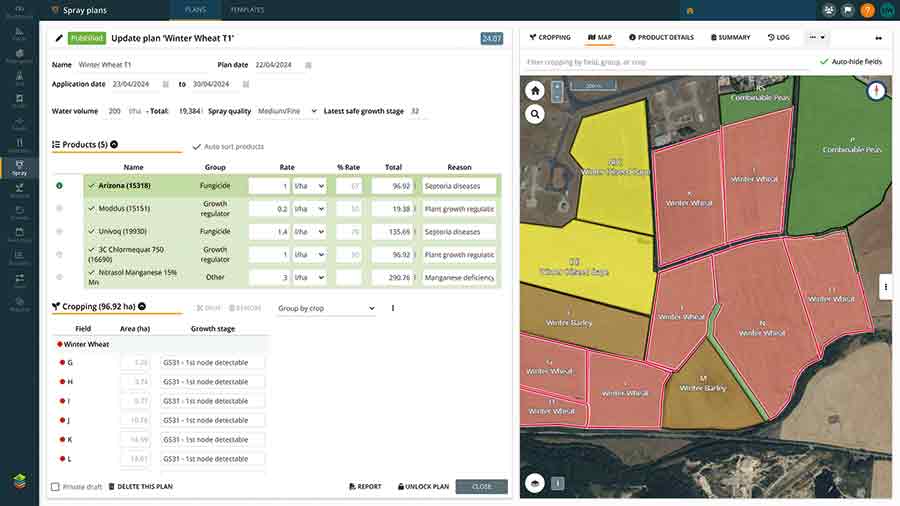
Stock management
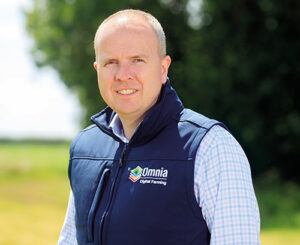
Hutchinsons has also included real-time stock management. Users will be able to monitor stock levels of fertilisers, seed and crop protection chemicals through Omnia.
Stores for products are created through the portal and products can be added or archived as they move in and out of use.
“We believe that the current systems capable of offering this are inflexible,” said Oliver Wood, precision technology manager. “It’s more important than ever to have full traceability and transparency, from ordering through to application.”
Users who purchase products through Hutchinsons will see the most functionality, with the module being linked to the company’s ERP system, meaning that orders are automatically logged and tracked through to delivery.
When using other suppliers, management can manually update the system to show new orders, orders out for delivery and products delivered. As products arrive on site, the allocated store is updated to show real-time stock levels.
Linking to both the field diary and production modules, when tasks are completed the stock levels are automatically updated and the gross margin calculations are adjusted based on the accurate price paid for products.
During stock takes, all transactions for individual stores are available to review. Pricing can be viewed either as a weighted average, a fixed cost or as the price of the last purchase.
Crop performance
Everything within the updated Omnia system feeds into the crop performance module, which provides real-time analysis of the profitability of each crop. Margins can be calculated at a whole-field or sub-field level, with the sub-field resolution showing the estimated cost per tonne based on the information available.
It’s also possible to adjust how this data is seen, breaking down information into variable or fixed costs, individual fields or crops, or on a whole-farm basis. This will enable more informed decision-making.
The new Omnia modules will officially launch at Cereals on 11-12 June, although it will be available to existing Omnia users from 7 June. The new functionality will be integrated at no additional cost to the end user, with three pricing tiers:
- Omnia Access Free of charge – full functionality of the field, map layers and data imports modules, and partial functionality of reporting, climate and scout app features
- Omnia Field Manager £3.15/ha – as above, but with full functionality and the addition of satellite imagery, pest and disease modelling, nutrition plans, seed plans and all new modules apart from the HALO audit
- Omnia Business Manager £6/ha – all functionality, including HALO auditing, and use of variable-rate prescription plans, field performance mapping and production cost analysis.